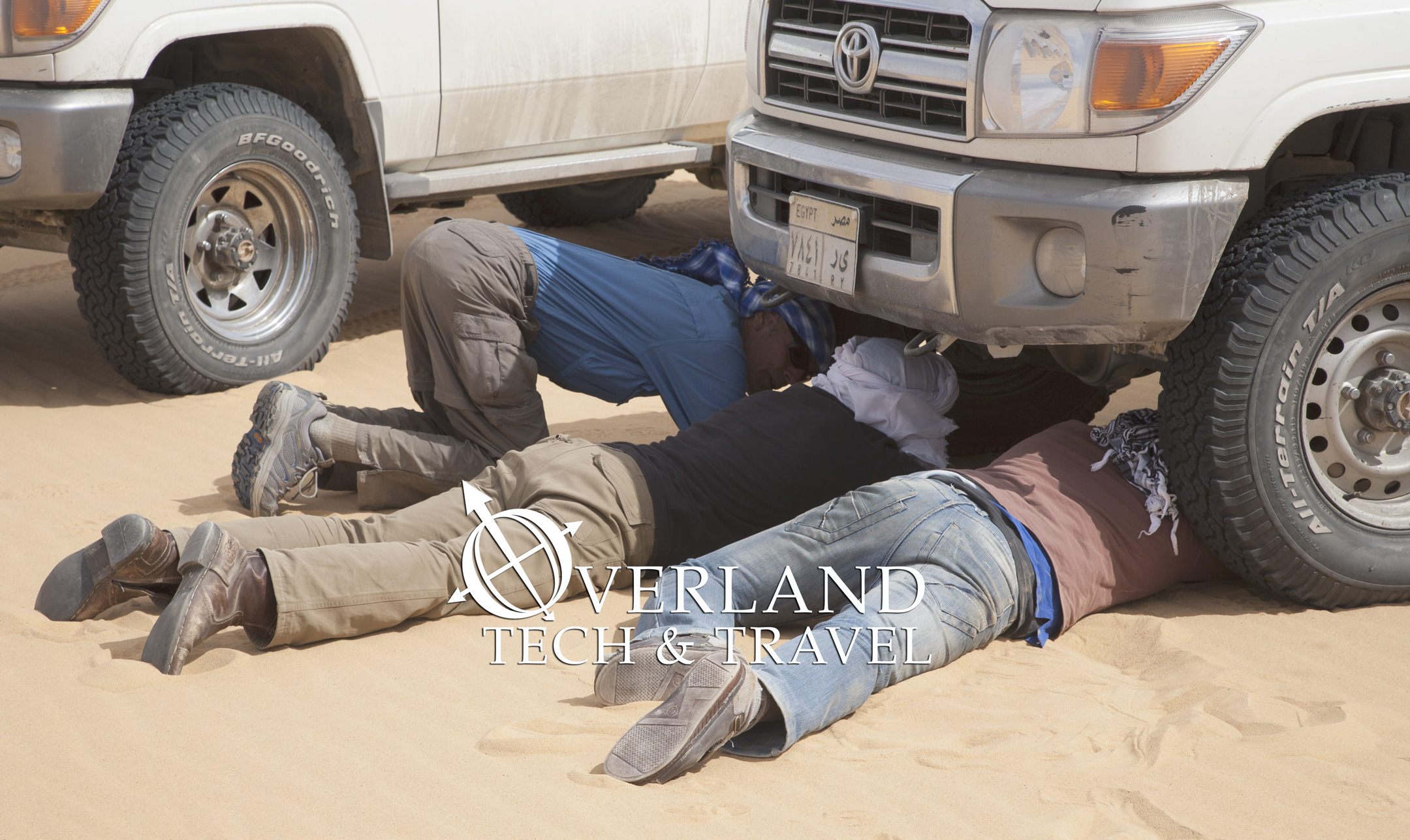
Overland Tech and Travel
Advice from the world's
most experienced overlanders
tests, reviews, opinion, and more
Mistaken mystique: myths of tire repair
Despite significant advances in technology and huge reductions in the frequency of failure (certain infamous Firestone models excepted), tires remain the number one cause of vehicle trouble, whether you’re driving your minivan to Disneyland or a Defender to Dodoma.
The minivan can get by with a single spare tire. For an expedition vehicle you need to think a little more comprehensively. A second spare is a good start, but the very best strategy is to combine that with the means to accomplish your own tire repairs. Fortunately there are many products available to make the job easier, if not always effortless.
A surprising number of the Land Cruisers Roseann and I see and use in Tanzania and Kenya still ride on stout, tube-type, 10-ply-rated bias-ply tires mounted on split rims (or, more properly, retaining-ring or locking-ring rims). I even ran this type of rim (with BFG All-Terrains) on my FJ40 for several years while guiding in Mexico. Such rims can be disassembled with hand tools to remove the tire and tube, but I found I experienced more flats with tubes, and the process to repair a simple puncture involved the same complete disassembly of the rim as a major sidewall split. I got really good at it, but it was still a pain, and the romance of having clients marvel at the procedure soon wore off.
Given todays’ availability of high-quality compressors, comprehensive tire-plug repair kits, and, for extensive sidewall repairs, various bead-breaking tools, there’s really no reason any more to use tubes or locking-rim wheels. Most simple punctures can be repaired with a plug while the wheel is still on the vehicle—I’ve repaired such holes before the tire had a chance to completely deflate.
It’s easy to become proficient at plug repairs with just a practice session or two, and that skill will handle probably 90 percent of tire problems you’ll encounter. But when presented with a tire that has popped its bead off the rim, or a serious sidewall split that demands repair from inside the tire carcass, most of us still become gripped with angst. Doesn’t reseating a bead involve flammable liquids and YouTube-prone explosive effects, or at the very least an air compressor or tank capable of producing a really big volume of air? Hundreds of posts on dozens of forums will tell you so. Even a video I recently watched from someone who should know better reinforced the idea that you need a big compressor and/or air reservoir to successfully reseat the bead on a tire.
The truth is, it just ain’t so. To prove it, I once reseated the bead on a 255/85 R16 tire using an Extreme Outback ExpeditionAire compressor, a clever product that employs a pair of toy-like AtomAire pumps each capable of no more than .9 cfm (cubic feet per minute) flow. Doing the same with any decent compressor is easy (although I won’t vouch for the $29.99 Costco variety).
Despite significant advances in technology and huge reductions in the frequency of failure (certain infamous Firestone models excepted), tires remain the number one cause of vehicle trouble, whether you’re driving your minivan to Disneyland or a Defender to Dodoma.
The minivan can get by with a single spare tire. For an expedition vehicle you need to think a little more comprehensively. A second spare is a good start, but the very best strategy is to combine that with the means to accomplish your own tire repairs. Fortunately there are many products available to make the job easier, if not always effortless.
A surprising number of the Land Cruisers Roseann and I see and use in Tanzania and Kenya still ride on stout, tube-type, 10-ply-rated bias-ply tires mounted on split rims (or, more properly, retaining-ring or locking-ring rims). I even ran this type of rim (with BFG All-Terrains) on my FJ40 for several years while guiding in Mexico. Such rims can be disassembled with hand tools to remove the tire and tube, but I found I experienced more flats with tubes, and the process to repair a simple puncture involved the same complete disassembly of the rim as a major sidewall split. I got really good at it, but it was still a pain, and the romance of having clients marvel at the procedure soon wore off.
Given todays’ availability of high-quality compressors, comprehensive tire-plug repair kits, and, for extensive sidewall repairs, various bead-breaking tools, there’s really no reason any more to use tubes or locking-rim wheels. Most simple punctures can be repaired with a plug while the wheel is still on the vehicle—I’ve repaired such holes before the tire had a chance to completely deflate.
It’s easy to become proficient at plug repairs with just a practice session or two, and that skill will handle probably 90 percent of tire problems you’ll encounter. But when presented with a tire that has popped its bead off the rim, or a serious sidewall split that demands repair from inside the tire carcass, most of us still become gripped with angst. Doesn’t reseating a bead involve flammable liquids and YouTube-prone explosive effects, or at the very least an air compressor or tank capable of producing a really big volume of air? Hundreds of posts on dozens of forums will tell you so. Even a video I recently watched from someone who should know better reinforced the idea that you need a big compressor and/or air reservoir to successfully reseat the bead on a tire.
The truth is, it just ain’t so. To prove it, I once reseated the bead on a 255/85 R16 tire using an Extreme Outback ExpeditionAire compressor, a clever product that employs a pair of toy-like AtomAire pumps each capable of no more than .9 cfm (cubic feet per minute) flow. Doing the same with any decent compressor is easy (although I won’t vouch for the $29.99 Costco variety).
Any quality compressor, such as this Quick Air X (sadly no longer available), is capable of reseating tire beads
Let’s imagine you’ve put a nice two-inch split in the outboard sidewall of a tire, but it’s still seated firmly on the rim. You need to get behind the split to apply a patch, which means you need to pop the bead off the rim first, then pry the edge of the tire off the rim. This is also a procedure viewed as black magic by many, but it’s easily done. (Before you attempt any of the following, don a pair of gloves and eye protection.) The most elegant way I’ve found is with a set of Tyrepliers, which comprise a lever system that angles between the bead and rim and pries the former off the latter with little fuss. The next most elegant way is with a product called a Beadbuster, a plate incorporating a curved spade that bolts to the bottom of a Hi-Lift jack. To use it, you place your tire and rim under the bumper of your vehicle, position the jack with the curved spade next to the rim against the bead, and use the jack with pressure against the bumper to force the bead downward and off.
These Tyrepliers, from Australia, make quick and elegant work of breaking a bead
Failing either of these accessories, the base of the Hi-Lift by itself will do the same thing; it just puts a bit more stress on the tire’s sidewall than you do with the Beadbuster. In fact, people have unseated beads by simply driving over the edge of the tire with another vehicle. Whatever technique you use, be sure to mark the tire and rim first so you can reposition the tire in the same place, preserving the balance. (If you’ve popped off both beads through overzealous hooning this obviously won’t be possible.)
Once the outside bead has popped off, it’s much easier to get the inside bead off. You’ll want to do this so you can position the inside bead in the center groove of the wheel. With that done, a pair of tire irons will enable you to pry the outside bead over the edge of the rim, at which point you can patch the split by reaching inside (taking the tire completely off the rim is possible, but much more difficult and rarely necessary).
The Beadbuster works in conjunction with a Hi-Lift jack
Once you’ve applied the patch and pushed the bead back over the edge of the wheel, it’s time to reseat the beads (if you’ve just popped one off while driving you’ll begin here). First, remove the valve core—once you’ve seated the tire you’ll re-install the core to completely inflate the tire.
Virtually all experts recommend running a ratchet strap around the circumference of the tire and cranking it tight. The theory is that this pushes the beads out against the rim to assist sealing. But when I compared the ratchet technique with using nothing at all during the course of mounting eight BFG tires on four Land Cruiser and four Land Rover steel rims, I could detect no difference whatsoever in effectiveness. If anything, I found it easier to position the tire correctly without the strap. Your results might vary (and if your wheels are too wide for your tires it could help), but I’ve stopped bothering with the strap.
Now comes the important part. Stand the tire and wheel upright so you can inspect both the inside and outside of the rim. You want the wheel centered as perfectly as possible inside the tire, so the gap between the edge of the rim and the tire is as even as possible all the way around, on both the inside and outside of the rim. If the rim sits cockeyed so that one edge is right against the tire and there’s a big gap opposite, it won’t matter how big a compressor you have; the air will simply escape.
Next, you’ll want some sort of liquid to lubricate the tire so it can pop over the rim’s grooves more easily. The very best is water mixed with some liquid soap or detergent, but plain water will do in a pinch (so will, my nephew reports, Keystone Light beer, which is certainly the best use to which you could possibly put that stuff). A squirt bottle makes it easy to wet the entire circumference on both sides, but just splashing it on works too. Be generous with the solution. Especially if it's the "beer." Next time bring liquid soap and better beer.
Connect your compressor’s chuck to the valve. The clamp-on style makes things easier, but it’s not mandatory. Get the air going in, and watch both sides of the tire. The soap solution will help locate any bad gaps; if you see one and the tire refuses to expand, stop and realign the rim. If you have everything right, though, you’ll see the tire start to expand outward on both sides. It won’t happen symmetrically, but as long as there’s a seal it won’t matter. One bead will snap on first—it almost always seems to be the outside one for me, but that might just be happenstance. In any case, you won’t miss it happening—it can make an alarmingly loud pop. As soon as the second bead pops on, remove the compressor. Air will come rushing back out through the coreless valve, but that’s of no consequence—the beads won’t come back off once they’re on.
Reinstall the valve core, inflate to normal pressure, and you’re finished. No fuss, no big compressor or air tank needed—and no YouTube-prone pyrotechnics.
If you’d like some excellent hands-on instruction in all facets of tire repair, sign up for the two-hour tire-repair class at the Overland Expo. Adventure motorcycle attendees will find equivalent classes from the qualified folks at RawHyde Adventures.
No poseur machine: Tiffany Coates' R80GS, Thelma
When legendary motorcycle world traveler Tiffany Coates was in the U.S. for a speaking tour in 2010, BMW Motorrad USA offered to pay for parts and repairs on her 20-year-old R80GS, Thelma, which by then had carried her well over 150,000 miles on five continents.
When Tiffany told her father the good news, his response was, “Bloody hell—had they seen the bike when they offered that?”
When legendary motorcycle world traveler Tiffany Coates was in the U.S. for a speaking tour in 2010, BMW Motorrad USA offered to pay for parts and repairs on her 20-year-old R80GS, Thelma, which by then had carried her well over 150,000 miles on five continents (TiffanysTravels.co.uk).
When Tiffany told her father the good news, his response was, “Bloody hell—had they seen the bike when they offered that?”
Indeed. A close (i.e. anything nearer than 50 feet) inspection of Thelma indicates that Tiffany pays diligent attention to the mechanical aspects of the bike, and pretty much files aesthetics under “patina.” A good third of the bumblebee yellow paint on the front guard seems to have been left in flakes in foreign countries, and various scrapes, gouges, blobs of third-world welds, and fraying wraps of duct tape attest to the drops and general wear unavoidable in the course of accumulating the spectacular CV of this motorcycle and its rider.
Tiffany will be at the 2012 Overland Expo, teaching classes in personal safety for women, contributing to regional travel forums and experts panels, and presenting a talk and slide show on central Asia.
Meanwhile, here’s a close look at Thelma, who’s been enjoying a break parked at the Overland Expo headquarters outside Tucson. If you haven’t yet seen Tiffany’s BMW Unscripted video clip, watch it here: http://www.youtube.com/watch?v=XAUhV1r-kUo
A bit of road wear is apparent on the lamp guard
Crash bars have some stories to tellThe modifications to Thelma are scant. Besides the much-repaired hard luggage mounts, here’s a comfortable Bill Mayer saddle, a custom Wilbers Suspension rear spring and shock, and, well . . . that’s about it.
Running gear is virtually stock
Single non-vented disc brake in front, drum in rear
Hey, it still blinks . . .
Underside shows the effects of 200,000 overland miles
Weld repairs would give a German engineer nightmares
But Mickey seems happy to ride along . . .
Speed vs. economy, or Fd = 1/2pv(squared) x CdA
Diesel engines such as this fine 1HZ are inherently economical, but they still have to work harder to push a vehicle faster Fuel economy is a funny subject. Very, very few people want to admit their vehicles get poor mileage. The overwhelming tendency is to fudge the other way when the subject comes up. I know for a fact there are guys who get 25 miles per gallon at 75 miles per hour in their one-ton diesel pickups while towing their 30-foot Airstream trailers, because I hear it with astonishing frequency.
I also know they don’t.
I never say as much when presented with these or similar absurd boasts, because there’s simply no profit in doing so. All I do is raise my eyebrows and say, subtly, “Wow. That would be impressive.” To show skepticism, much less outright derision, provokes the same peculiar outrage one receives doubting someone who claims to have been abducted and studied by aliens. There’s just no point in arguing.
There’s also no point in arguing with the laws of physics—especially those relating to speed. Note that formula in the headline. In plain English it states that the drag (Fd) on a solid object moving through a fluid medium (which in physics includes air) is a function of one-half the density (p) of the medium times the speed (v) of the object, squared, times the drag coefficient (Cd) of the object times its cross sectional area (A).
Note in particular the reference to the square of speed. That means that as speed goes up, the drag that results rises on a logarithmic curve. If speed doubles, drag quadruples.
Diesel engines such as this fine 1HZ are inherently economical, but they still have to work harder to push a vehicle faster Fuel economy is a funny subject. Very, very few people want to admit their vehicles get poor mileage. The overwhelming tendency is to fudge the other way when the subject comes up. I know for a fact there are guys who get 25 miles per gallon at 75 miles per hour in their one-ton diesel pickups while towing their 30-foot Airstream trailers, because I hear it with astonishing frequency.
I also know they don’t.
I never say as much when presented with these or similar absurd boasts, because there’s simply no profit in doing so. All I do is raise my eyebrows and say, subtly, “Wow. That would be impressive.” To show skepticism, much less outright derision, provokes the same peculiar outrage one receives doubting someone who claims to have been abducted and studied by aliens. There’s just no point in arguing.
There’s also no point in arguing with the laws of physics—especially those relating to speed. Note that formula in the headline. In plain English it states that the drag (Fd) on a solid object moving through a fluid medium (which in physics includes air) is a function of one-half the density (p) of the medium times the speed (v) of the object, squared, times the drag coefficient (Cd) of the object times its cross sectional area (A).
Note in particular the reference to the square of speed. That means that as speed goes up, the drag that results rises on a logarithmic curve. If speed doubles, drag quadruples.
Here’s an example using an algorithm I found recently, calculated around a theoretical but representative vehicle with a drag coefficient of .30 (very low), and a frontal area of 30 square feet, on a paved road. Our vehicle requires just 2.6 horsepower to move at 20 mph. To reach 40 mph it needs 8.2 horsepower, and to reach 60 it needs 19.6. To cruise at 80 would require 39.9 horsepower—twice that needed to maintain 60. (To give you an idea of the drag acting on very high-performance sports cars, our vehicle would need 521 horsepower to hit 200 miles per hour.) The unassailable fact of highway driving is that beyond about 40 miles per hour aerodynamic drag overtakes powertrain friction and rolling resistance as the chief factor in fuel consumption—and from there on up it wages a rapidly escalating war on the level in your tank.
Another . . . interesting . . . claim I’ve heard is from guys (mileage fudging seems to be strictly a male pastime) who say something like, “I get better mileage at 80 than at 60 because my engine is in its power band there.” Sorry, but nonsense. There might be situations in which, say, shifting from fourth gear at 55 mph into an overdrive fifth gear and adding a few miles per hour will do no harm to or perhaps even slightly improve economy, but for a given gear, adding speed will increase fuel consumption, plain and simple. No one is going to get better gas mileage at 80 than at 60.
Algorithms are all well and good, but accurate real-world figures are more difficult to locate. Fortunately one of my best friends, Michael Cox, is diligent about recording the mileage he achieves with his 2006 4WD Dodge 2500 pickup, which has the Cummins turbodiesel, a six-speed manual transmission, and BFG All-Terrain tires. He can just break 21 mpg at 55 miles per hour. At 60 it drops to 19.5, at 65 it’s down to 18, and 70 mph knocks off another mile per gallon. He recorded similar changes with his Four Wheel Camper on the truck: 18.5 mpg at 60 mph, 16.5 at 65, and 15.5 or less at 70.
The immediate lesson from all this is so obvious I won’t bother to state it. But more subtle contributors to drag are worth investigating. Cleaning up the aerodynamics of a vehicle can have a significant effect on fuel economy, even on one with the base Cd of an apartment building. Removing the tall porthole ConFerr roof rack on my FJ40 increased my highway (i.e. 60 mph) fuel economy by a full one mile per gallon—and going from 16 mpg to 17 in an FJ40 is a blessing. Suspension lifts and wider tires increase drag, the former hugely. So, somewhat surprisingly, do such add-ons as bull bars and driving lights, which create a dirty front of turbulence before the air even hits the vehicle proper. Extreme example: When my nephew Jake exploited his newfound skills at welding and fabricated an exoskeleton roll cage for his V6 Tacoma, his mileage plummeted from 18 to 13 mpg. So, do you really need a fat grille bar to fend off stray kangaroos, or would you be served with a simple winch bumper? Do you need that Paris/Dakar-esque bank of driving lights, or would a headlamp upgrade provide all the safe illumination necessary? With gasoline poised to top $4.00 per gallon and diesel above that as I write this, every bit will help on a long highway trip.
Ditching the roof rack helps. Brush guard and lights might not hurt the “aerodynamics” of an FJ40, but they can on a more streamlined vehicle.Although rolling resistance becomes less important than aerodynamic drag at high speeds, it’s still worth considering. That one mile per gallon I gained on my FJ40 made up for the exact same amount I lost when I switched from BFG All-Terrains to BFG Mud-Terrains on that vehicle. Long experience with various tread types has led me to the conclusion that there’s not a big mileage difference between street/trail tread patterns such as BFG’s Rugged Terrain and the slightly more aggressive All-Terrain—but jumping to a Mud-Terrain you’ll take a quantifiable hit. So if you put mud-pattern tires on your vehicle just because you like the look, think again. You’ll get better mileage, better handling, a better ride, and longer tread life with an all-terrain pattern, probably equivalent traction in most circumstances, and better in some.
What about tire width? Wider tires certainly increase frontal area and drag, but I’ve never seen an authoritative study to determine if a wide but short contact patch produces more rolling resistance than a longer, narrower one. You’d need to determine loading per square inch, hysteresis of the carcass, heat buildup, and other factors to make a solid judgement. With that said, I believe narrower tires offer advantages in so many other areas that I invariably stick with unfashionably skinny sizes. I just spent two weeks in Egypt’s sand seas in gargantuan Land Cruiser Troopies riding on pizza-cutter 235/85x16 All-Terrains, and we were never more than nominally stuck despite running near-street pressure in areas mined with the razor-sharp limestone outcroppings called kharafish.
Narrow tires reduce frontal area and possibly rolling resistance, and they work just fine in sand if aired down properlyThe unique characteristics of individual vehicles can make a difference in fuel economy as well. For example, my mechanic friend Bill Lee had a customer who drove an FJ60 with a five-speed conversion, who complained of wildly varying mileage on the highway in the 60-65 mph range. Bill figured out that the secondary venturi on the 2F engine’s two-barrel carburetor started opening at around 63 miles per hour. If the driver kept the speed just below that, mileage was a full two or three miles per gallon better than just above it.
Modern fuel-injected engines are unlikely to have such a sharp break in efficiency. Nevertheless, it’s worth experimenting with varying speeds—especially if you have a mileage function on your vehicle’s computer—to see if it has a “sweet spot” above which consumption spikes.
In general though, you can expect your computer to tell you, “Yep—when you drive faster you use more fuel, stupid.”
Hint: When using “Search,” if nothing comes up, reload the page, this usually works. Also, our “Comment” button is on strike thanks to Squarespace, which is proving to be difficult to use! Please email me with comments!
Overland Tech & Travel brings you in-depth overland equipment tests, reviews, news, travel tips, & stories from the best overlanding experts on the planet. Follow or subscribe (below) to keep up to date.
Have a question for Jonathan? Send him an email [click here].
SUBSCRIBE
CLICK HERE to subscribe to Jonathan’s email list; we send once or twice a month, usually Sunday morning for your weekend reading pleasure.
Overland Tech and Travel is curated by Jonathan Hanson, co-founder and former co-owner of the Overland Expo. Jonathan segued from a misspent youth almost directly into a misspent adulthood, cleverly sidestepping any chance of a normal career track or a secure retirement by becoming a freelance writer, working for Outside, National Geographic Adventure, and nearly two dozen other publications. He co-founded Overland Journal in 2007 and was its executive editor until 2011, when he left and sold his shares in the company. His travels encompass explorations on land and sea on six continents, by foot, bicycle, sea kayak, motorcycle, and four-wheel-drive vehicle. He has published a dozen books, several with his wife, Roseann Hanson, gaining several obscure non-cash awards along the way, and is the co-author of the fourth edition of Tom Sheppard's overlanding bible, the Vehicle-dependent Expedition Guide.