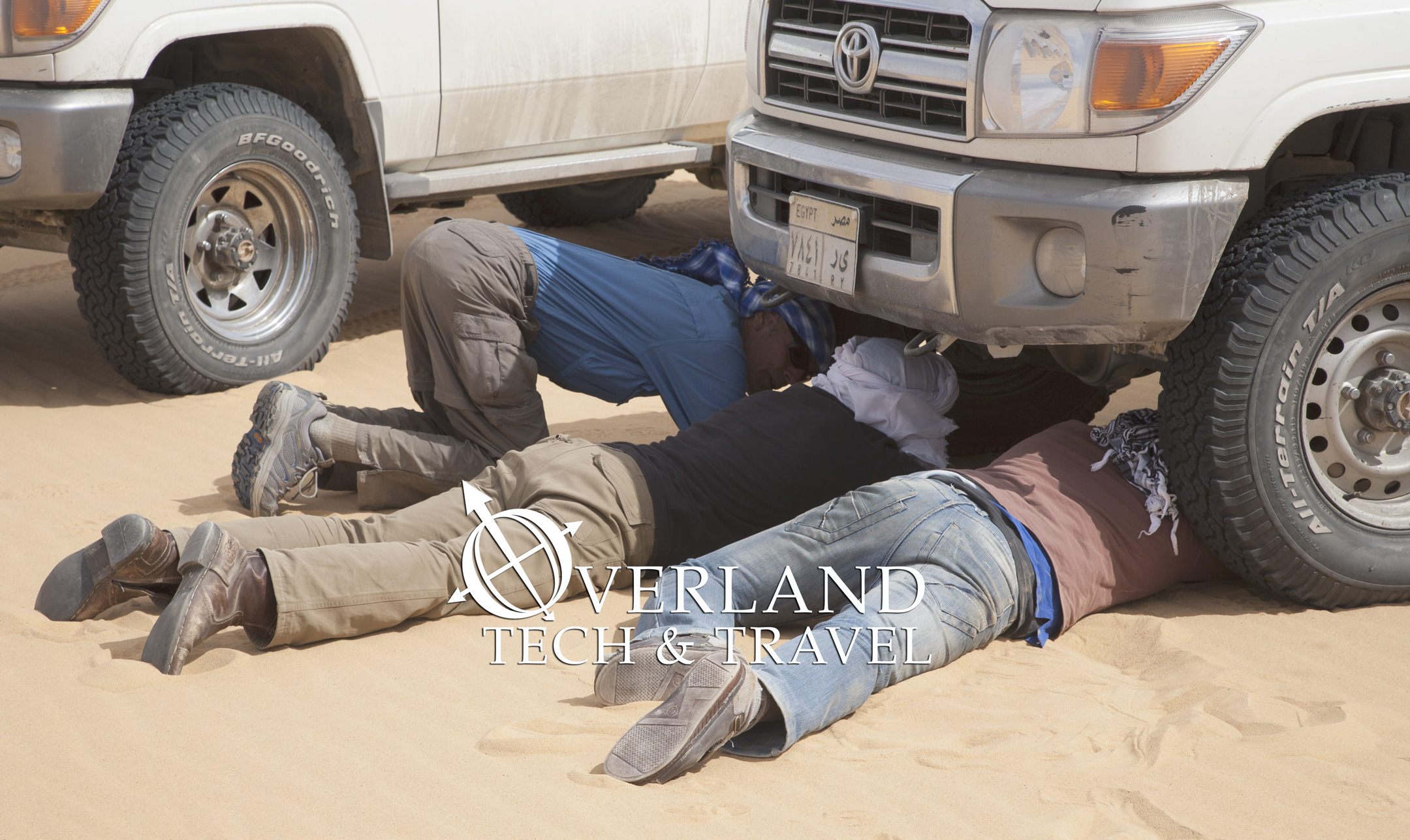
Overland Tech and Travel
Advice from the world's
most experienced overlanders
tests, reviews, opinion, and more
Parabolic springs: What exactly are they?
ARB/Old Man Emu recently announced, with great fanfare, a rear suspension kit for the 70-Series Land Cruisers that includes a two-leaf parabolic spring for each side, plus adjustable air bags to compensate for overload conditions. It can replace a standard semi-eliptic spring pack that might require 12 or more leaves to support an equivalent load.
Other manufacturers, such as Terrain Tamer, have also introduced parabolic springs kits for 70-Series Land Cruisers, as well as Series II and III Land Rovers.
But what exactly is a parabolic spring? And is it really better than a standard leaf spring?
The individual leaves of a standard, semi-eliptic, multi-leaf spring pack are stamped and then bent from strips of heat-treated, medium- to high-carbon steel, more or less rectangular in cross section, and of consistent thickness and width the length of the leaf (except for, in some cases, when the ends are rounded or have the corners relieved). When attached to a simple pivot at one end, with the other free to rotate a movable shackle, a single leaf resists bending in a fairly uniform fashion throughout its travel. To increase strength—that is, load-carrying ability—and add progressive resistance, progressively shorter leaves are added beneath the top leaf, held loosely in place with floating brackets that do not restrict movement. As the spring pack is compressed, each leaf slides against the adjacent leaves. This inter-leaf friction results in a self-dampening effect—unlike, for example, a coil spring, which has little internal resistance and relies almost entirely on a shock absorber (damper) to control oscillations.
However, that inter-leaf friction also degrades the ride quality of a leaf spring as well as its compliance—the ability to compress or extend fully. And this effect worsens as the spring gets dirty and/or rusty. Some manufacturers (such as OME) install replaceable anti-friction pads at the leaf tips, which help noticeably but do not eliminate the problem.
Years ago a few manufacturers—among them Nissan—attempted to create a progressive-rate leaf spring by making the leaves thicker in the middle, tapering in a linear fashion to the tips, as in the (very) simple schematic below. This involved a relatively easy manufacturing process. However, these “taper-leaf” springs proved less than ideal as bending stresses were not evenly distributed through the length of the leaf, resulting in weak points and failures.
Enter the parabolic spring.
While it’s difficult to discern looking at it from the side, the thickness taper of a parabolic spring follows a complex mathematical formula. Rather than simply tapering straight from the center of the leaf to the end, a parabolic spring looks like an extremely stretched-out version of the illustration below. As you might imagine, it’s significantly more difficult—i.e. expensive—to design and manufacture than simply stamping out flat lengths of steel and piling up enough of them to support a load.
The results, however, are worth it. Not only is a parabolic leaf progressive in its operation, it is also nearly as compliant as a coil spring due to the lack of internal friction and stress. Theoretically a single parabolic leaf would be sufficient to function as a spring; however, due to the ramifications if the leaf did break, most parabolic spring kits for vehicles comprise at least two leaves, and the lower leaf will have a full military wrap on each eye, to contain the upper spring should it break. These leaves touch only at the spring seat in the middle, and at the ends, so there is virtually no interleaf friction. Most kits also include a free-floating overload leaf that only engages under high load or compression. The illustrations below are from a (densely technical) Researchgate-published paper on leaf spring design, available to read or download here.
There’s more: A parabolic spring equivalent in load-carrying capacity to a standard multi-leaf spring weighs at least 30 percent less, drastically reducing unsprung weight and further improving ride and handling. Convert an all-leaf-sprung vehicle to parabolics and you could take 80 pounds off its total mass.
The conversion job is straightforward, no more complex than changing out standard springs, although the vehicle will almost certainly require new, firmer shocks to compensate for the loss of inter-leaf friction. Series Land Rover owners I know who’ve converted describe it as “transformative.” This diagram shows the magnitude of travel possible with a parabolic spring system, as well as the longitudinal “S” deformation any leaf spring undergoes during severe braking.
While it’s easy to find parabolic spring kits for Series Land Rovers and the 70-Series Land Cruisers, diligent searching revealed no such kits for my FJ40, although I heard that one company did offer them for a while years ago. Damn.
Incidentally, there is no relation between the terms “semi-elliptic” and “parabolic” in leaf spring terms. Semi-elliptic refers to the shape the entire spring pack assumes from the side; if one were to draw this shape out into a connected oval, it would be roughly elliptical. A parabolic vehicle spring pack assumes this same profile and is thus also semi-elliptical.
OME MT64: OME's answer to Bilstein?
My FJ40 has sat atop ARB’s Old Man Emu suspension for over 20 years, and our HZJ75 Troop Carrier is equipped with it as well. OME leaf springs—selectable for varying permanent loads from stock to heavy-duty—improve on the ride offered by factory springs while offering more load-carrying ability. And OME’s twin-tube, low-pressure nitrogen-charged Nitrocharger shock absorbers—or dampers to use the technically correct term (not “dampener”)—have never failed us or shown signs of fade, even on day-after-day-long stretches of Australian corrugations.
So I am understandably an OME fan, and I pay attention to new developments. I wasn’t surprised when the company introduced their ultra-premium, internal-bypass, BP51 shock—it made sense to go head to head with such brands as Fox and Icon, with a shock that incorporated high-performance technology to better the Nitrocharger’s ride at low to moderate speeds while also bettering its high-amplitude damping. If the BP51 were available for our Troopy I would seriously consider spending the cash to upgrade.
I was surprised, however, to learn about OME’s new shock, the MT64 (MT64 referes to monotube construction and the shock’s stout 64mm diameter piston). I’ve watched in the past as companies diluted their product lines with so many choices that consumers simply gave up trying to understand the differences and switched to another brand. ARB descibes the MT64 as sitting between the Nitrocharger and BP51 in performance and price.
Hmm. I looked at the specs. Indeed the MT64 splits the difference in price. But is there really a need for a shock that is “halfway” between the two in performance? I looked at the construction, which is neither the twin-tube, low-pressure design of the Nitrocharger nor the internal-bypass (or any bypass at all) of the BP51, but a monotube, high-pressure gas-charged format. In its front strut configuration it offers adjustable ride height.
Then it hit me: The MT64 is OME’s alternative to Bilstein.
Bilstein shocks have long been a popular upgrade to factory shocks—they’re reasonably priced, offer definite performance gains, and carry a storied name to boot. The Bilstein 5100 is a common swap; more recently, the beefier 6112 front strut assembly has become the go-to shock for those with typically overloaded overland rigs.
Consider the MT64 front strut assembly alongside the 6112: Both are monotube, high-pressure gas-charged units with enlarged oil/gas capacity, a floating piston to contain the nitrogen gas, and adjustable ride height. For fans of high-pressure gas-charged shocks, the MT64 offers an obvious alternative to Bilstein. So how do they compare in terms of specifications?
The MT64’s piston is 64mm in diameter (it’s actually 63.5 but that’s not very catchy); the shaft is 22.2mm in diameter. The (monotube, remember) aluminum body is 71mm across.
The Bilstein 6112 has a 60mm piston and an 18mm shaft, in a steel body 67.3mm in diameter.
I see what you did there, OME. The MT64 is just a bit beefier in every dimension, a contrast that will play well in comparison tests—and likely on the trail as well. Visually, the MT64’s forged aluminum body caps also appear sturdier than those on the 6112. I liked the plastic guard over the shaft, which should help protect it from grit blasting (although not as well as the full cover on the Nitrocharger), and the natural rubber bushings rather than wear-prone heim joints.
There’s one other important difference: The MT64 is fully rebuildable; the Bilstein 6112 is not.
The MT64 is offered in both strut and standard configurations, so you can run the same basic shock on strut or conventional front suspensions, and the rear as well. The Bilstein 6112 is only offered as a strut assembly for front suspensions; for rear shocks most will choose either Bilstein’s B8 5100, a significantly smaller unit with a 14mm shaft and a 46mm piston, or the B8 5160, essentially the 5100 with the advantage of a remote reservoir.
Perhaps what is more important than the differences between these two shocks is what they share in common: their target audience.
High-pressure gas-charged shocks such as these and similar models are marketed toward those who want more of a sporting—i.e. firmer—initial response in ride and handling, compared to a typical twin-tube, low-pressure design. Advertising descriptions usually include references to “spirited” driving, and promo videos rarely fail to show at least a few scenes with two if not all four wheels in the air. It is, sadly, a typical approach: Manufacturers make lots of noise about “treading lightly” while overtly encouraging just the opposite.
Not too long ago I watched a (very well-filmed) video about a group of guys playing Ivan Stewart with several overland-kitted vehicles on a (public) dirt road in Baja—a route I know well. Lots of whooping and flying gravel, and inset frames boasting their current speed. One of them finally managed to stuff his friend’s Jeep Gladiator into the desert and fold the chassis into a notable inverted V. Incredibly, rather than slinking home and considering a different approach to traveling in a foreign country, they went right on partying as if this were an unfortunate but completely normal contingency for a bro excursion. Sadly, this video—and the attitude—is far from unique.
Sorry, where was I? Right: If you travel like I do, with mechanical sympathy for your vehicle uppermost in your mind, enjoyment of your surroundings second, and preservation of the environment and the trail a close third, you don’t need shocks that can shrug off repeated jumps. If you prefer the slightly sharper on-road handling high-pressure gas shocks provide, that’s great. But for comfortable, reliable, long-distance travel, a well-built twin-tube shock such as the OME Nitrocharger, properly specced to your constant load, will serve you well. If you want a more sophisticated ride, as well as the ability to adjust both compression and rebound damping—and you have the funds—then by all means spring for the superb BP51.
Hint: When using “Search,” if nothing comes up, reload the page, this usually works. Also, our “Comment” button is on strike thanks to Squarespace, which is proving to be difficult to use! Please email me with comments!
Overland Tech & Travel brings you in-depth overland equipment tests, reviews, news, travel tips, & stories from the best overlanding experts on the planet. Follow or subscribe (below) to keep up to date.
Have a question for Jonathan? Send him an email [click here].
SUBSCRIBE
CLICK HERE to subscribe to Jonathan’s email list; we send once or twice a month, usually Sunday morning for your weekend reading pleasure.
Overland Tech and Travel is curated by Jonathan Hanson, co-founder and former co-owner of the Overland Expo. Jonathan segued from a misspent youth almost directly into a misspent adulthood, cleverly sidestepping any chance of a normal career track or a secure retirement by becoming a freelance writer, working for Outside, National Geographic Adventure, and nearly two dozen other publications. He co-founded Overland Journal in 2007 and was its executive editor until 2011, when he left and sold his shares in the company. His travels encompass explorations on land and sea on six continents, by foot, bicycle, sea kayak, motorcycle, and four-wheel-drive vehicle. He has published a dozen books, several with his wife, Roseann Hanson, gaining several obscure non-cash awards along the way, and is the co-author of the fourth edition of Tom Sheppard's overlanding bible, the Vehicle-dependent Expedition Guide.