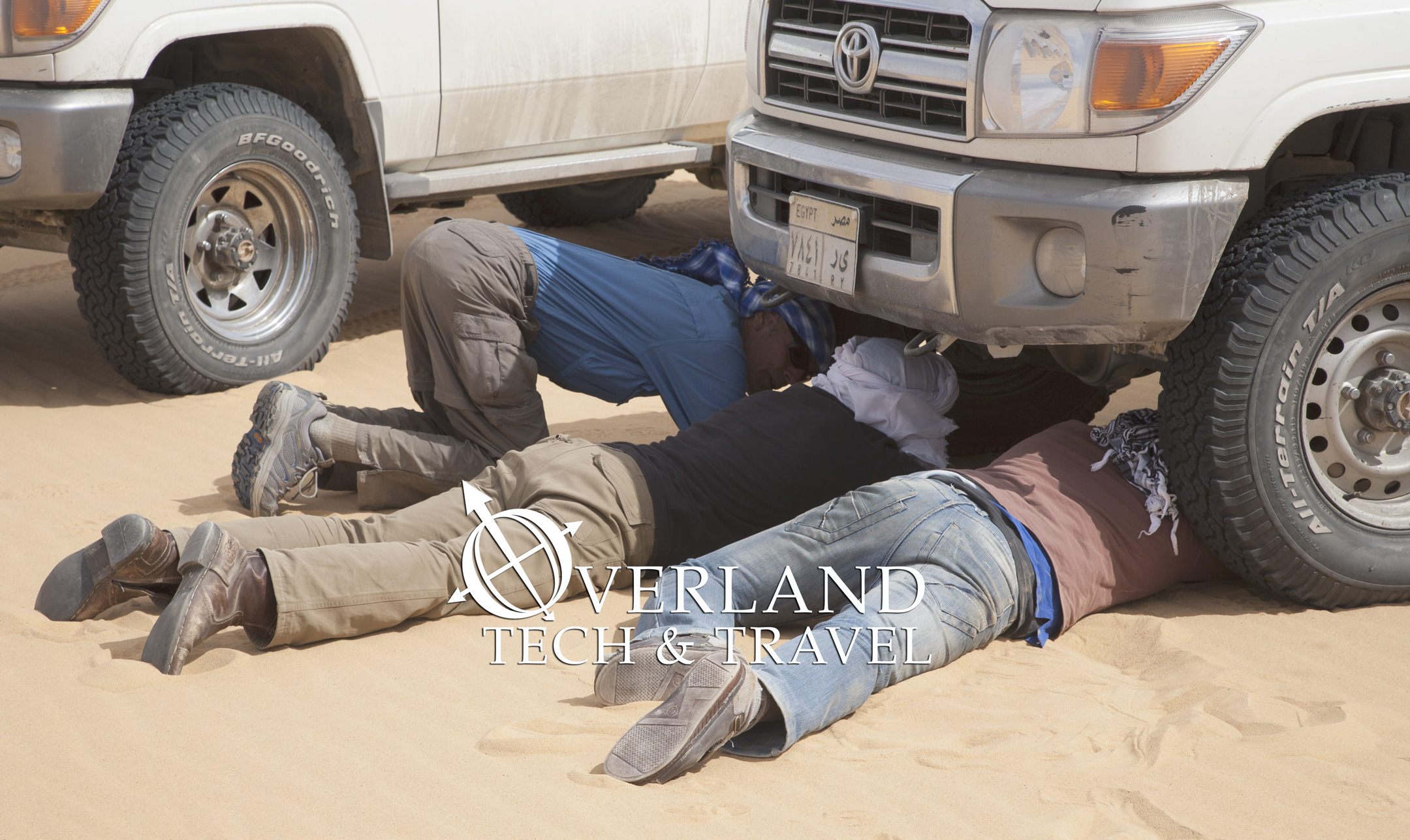
Overland Tech and Travel
Advice from the world's
most experienced overlanders
tests, reviews, opinion, and more
Not quite ready for prime time . . .
Any time you can reduce the potential kinetic energy in a winch system it is a Good Thing. PKE, as we’ll call it, comprises any part of the system that could become a projectile in the event of a failure of itself or any other component. In the vast majority of winch mishaps it’s the line that breaks, but shackles, shackle mounts, tree straps, even entire bumpers are unlikely but potential sources of high-velocity widow-making destruction.
The advent of synthetic winch line reduced the risks inherent in winch recovery by an order of magnitude. Although they both display about the same amount of stetch under load (less than one percent), synthetic winch line—typically SK-75 Dyneema—weighs one seventh of the same length and load-rated steel cable, and its 12-strand woven construction prevents the violent untwisting motion that occurs when a steel cable breaks. (For much more on steel versus synthetic winch line, see here.)
Recently, several companies have introduced soft shackles made from material identical to synthetic winch line. Soft shackles lock via a deceptively simple-looking turks’ head knot on one end and a spliced loop on the other—no threaded pin, in fact no metal at all. As with Dyneema winch line, the mass of the part is hugely reduced, along with its PKE. (Report soon.)
One frequently used winch accessory, however, stubbornly retains its mass: the pulley block, or snatch block, used to construct a redirected pull or increase the pulling power of the winch. Since the pulley itself must be of significant diameter to avoid damaging the line, the cheek blocks that support it must also be large and stout, and the axle of sufficient diameter to ensure a suitable working load limit (WLL) with a substantial safety margin. As a result, for example, even ARB’s excellent “Ultra Lite” winch pulley weighs 5.3 pounds, and their standard pulley is close to eight pounds.
That’s now changed—at least somewhat—with Research In Recovery’s aluminum Recovery Blok (sic). At four pounds even, the RIR pulley boasts a 25 percent reduction in mass over ARB’s lightest model.
To be honest, that 1.3-pound savings represents less of a safety enhancement than a simple reduction in handling weight. If you’re ever unspooled 75 feet of steel winch cable up a hill while carrying several steel shackles, a tree strap, and a standard steel pulley block you’ll appreciate this. Still, if the worst happens and you find a winch pulley headed toward you at 40 feet per second or so, better it weighs four pounds than five and a quarter . . .
Since such accidents in a properly set up and monitored winch system are vanishingly rare, let’s look at the RIR pulley from a practical point of view, first giving due credit to the welcome lightness. Next up of note is the very fine production quality. The body of the pulley is beautifully machined billet 6061 aluminum, given an attractive tumbled finish. All the edges are rounded, and shallow raised ridges protect the ends of the stainless-steel axle, which is secured with external snap rings for ease of maintenance and cleaning. The polymer pulley is smooth and spins easily; its semi-circular groove is 1/2-inch wide, thus suitable for most winch lines.
The cheek blocks are finely finished exactly flush with the edge of the pulley; this is attractive but, as Camel Trophy veteran Duncan Barbour pointed out when I showed it to him, would fail to protect the line from abrasion if the pulley wound up vertically in contact with the ground or a rock with line being pulled through it. The ARB Ultra Lite pulley incorporates shoulders on the flanks of the pulley which would help prevent this. If the Recovery Blok’s cheek blocks extended even a quarter inch there would be enough stand-off space to provide some protection.
Of more potential hassle is the securing hole at the head of the unit. It is sized so that only the pin of a shackle will fit through it, not the loop. Thus, for example, if you wanted to attach the pulley to a typical winch bumper, the shackle mounts of which also only take the pin of the shackle, you’d need to insert a second shackle, loop to loop, to connect the RIR pulley—thus negating all your reduction in PKE and handling weight. This wouldn’t be a factor if, say, you’re rigging a redirected pull off a tree using a tree saver strap. The loop of the shackle will fit through the loops in the strap, and the pin can then secure the pulley. (A soft shackle fits as well.)
Last to consider, but far from the least important, is the working load limit and breaking strength. WLL of the Recovery Blok is 20,000 pounds, identical to that of the ARB Ultra Lite unit (and superior to their standard pulley), and suitable for winches in the 9,000 to 12,000-pound range.
Unfortunately—critically, in fact—Research in Recovery does not yet know the breaking strength of the Recovery Blok. ARB lists the breaking strength of the Ultra Lite pulley at 38,500 pounds—nearly a two-to-one safety margin. While it’s possible the RIR pulley will exhibit a similar margin once it is tested (the company says they should have the information by the end of the year), without a solid figure it would be foolish to assume it is anything above the WLL, and that is insufficient for a piece of equipment that will be employed in potentially hazardous situations. Despite the high quality of the RIR pulley and its welcome weight savings, until I see a documented safety factor I can’t recommend it. I’ll update here if I learn more.
RIR is here.
The winch that wouldn't work
My friends are always sending me photos of vehicles they know will intrigue (or horrify) me. Most Series I, II, and III Land Rovers fit in the former category (although there are exceptions). The one here, spotted by Bruce Douglas in Seattle, looked nearly perfect at first glance—mostly stock, not quite concours and thus drivable without angst, lovely contrast of the dark green bodywork and tan hood, proper skinny tires on factory wheels.
The aftermarket seats were a bit much, although given stock Series II seats somewhat understandable—but why not just install the appropriate and excellent Defender items? Still it was a striking vehicle.
Then I noticed the winch.
Like quite a few early Land Rovers, this one was equipped with a capstan winch (whether from the factory or added later is impossible to say). A capstan winch differs from the more modern and much more common horizontal drum winch in having an upright drum, or capstan, like a winch on a sailboat. The capstan is powered by the engine, normally via a driveshaft connected to the front of the crankshaft. Unlike your Warn, Ramsey, or Superwinch, the capstan winch is designed to be used with a free length of rope, which is attached to the object to be winched (or to an anchor if winching the vehicle itself) and then wound around the capstan three or four times to provide friction. When the capstan is engaged, the operator pulls the free end of the rope to provide tension, and the capstan pulls in the attached end at slow speed. The advantage to this system is that there is no practical limit to the length of rope—if you need a 200-foot pull for some reason and have a 220-foot length of suitable rope, you’re good to go. It will also work as long as the engine is running, without overheating the winch or overtaxing the alternator. Disadvantages include limited power (most were rated at just 3,000 pounds, suitable for the 3/4-inch manila rope used) and the fact that if the engine isn’t running the winch isn’t either. Finally, solo recovery of a bogged vehicle is extremely awkward if not impossible. These downsides explain why capstan winches have been almost universally superceded by much more powerful horizontal drum winches that store their own line.
But the capstan on the Seattle Land Rover was—bewilderingly—wound with a long length of steel cable. This configuration cannot possibly function properly. You cannot use steel cable on a capstan as it is intended to be used—there would not be enough friction on the capstan and you would find the cable impossible to grip. And you cannot attach the free end of a steel cable to the capstan and expect it to wind in like a horizontal drum. It simply wouldn’t work and would likely destroy the winch in short order if it didn’t result in some much more serious failure. Note the horizontal bar on the mount, under which the rope is designed to run to properly feed it on to the capstan. Even if you managed to attach the steel cable and attempted to winch with it, it would instantly bunch up at the bottom of the capstan.
I’m at a complete loss to explain what the owner of this otherwise fine vehicle was thinking. I suspect he or she had no idea how a capstan winch worked and, seeing the steel cable attached to many horizontal winch drums, ordered one and somehow managed to attach and spool it on this poor capstan. To the uninformed it might look cool, but one can only hope its owner never attempts to put it to use for anything other than posing in front of some well-known Seattle coffee shop.
Why are there oranges in my tires?
You’ve no doubt seen racing drivers on a warm-up or yellow-flag lap weaving from side to side to keep their tires warm. The reason is that the rubber compound in race tires is formulated to be at its stickiest at race speeds and elevated temperatures. At cooler temperatures it quickly hardens and loses grip.
You could fairly state that designing a racing tire is simple compared to designing a tire for a street car or SUV. The racing tire only has to last long enough to finish the race, and often not even that long. Fuel economy is well down the list of priorities; ride comfort and noise aren’t even on it.
Not so with a street or SUV tire. Consumers want it all: long tread life and superior cornering traction, high fuel economy and safe braking performance, good off-pavement traction and low noise on pavement. A bunch of mutually exclusive characteristics. As you can imagine, a tread compound hard enough to last 40,000 or 50,000 miles and exhibit low rolling resistance to save fuel has a difficult time also providing above-average cornering and braking traction. Thus since the dawn of pneumatic tires manufacturers have juggled rubber and petroleum compounds to arrive at the best compromise for the application.
A few years ago Yokohama threw a new ingredient into the mix: orange oil, which, just as its name suggests, is derived from the oil in orange (and other citrus) peel—the specific compound desired is called limonene. Why citrus oil? One reason is to save on petroleum, of course, making the tire more “green.” But Yokohama claims a far more immediate benefit. According to the company, the tread compound in a tire constructed with limonene has the ability to instantly change viscosity in response to temperature. During normal driving the viscosity is high, resulting in low rolling resistance and long tread life. But during braking or cornering the viscosity shifts to a more sticky state, enhancing grip.
Proving or disproving this through independent testing might be difficult, since Yokohama does not offer otherwise identical tires with or without the orange oil technology. Most likely only a long period of consumer feedback and real-world tread-wear results will show if the concept is sound or just a marketing gimmick. The company gave me a set of the new Geolandar AT GO15 tires for our Ford F350 pickup, and so far they are performing excellently, with decent off-pavement traction and fine on-road characteristics. I just towed a 9,000-pound trailer full of Overland Expo equipment across the country, and had zero issues with handling or braking—including a couple of abrupt maneuvers to avoid insane suicidal drivers on the freeway through Dallas at rush hour (not fun at the wheel of 15,000 pounds worth of kinetic energy). The tread still appears within new specs, so I won’t be surprised if they last the full 50,000 miles promised by the guarantee. (The lighter-duty P/E Metric versions of the tire have a 60,000-mile warranty.)
I can’t find any other manufacturers using orange oil technology yet. I’m not sure if this is because Yokohama has managed to protect their use of it, if the others are sitting back to see how it goes, or if they are frantically testing their own citrus concoctions. Time will tell.
A proper shovel
While equipping our Land Cruisers for a trip across the Simpson Desert, we picked up a cheap shovel at a military-surplus-cum-Chinese-camping-gear store in Sydney. Just how cheap became apparent the first night we tried to dig a fire pit. The shovel literally bounced off the ground—the blade simply bent and sprang back under any force at all. It was so bad all we could do was laugh.
That won’t happen with this one.
We needed indestructible shovels for the Camel Trophy Skills Area at the Overland Expo, and a short web search convinced me that those from Wolverine Hand Tools fit the bill perfectly.
If you name a shovel “Wolverine” it had better be tough, since its namesake is known for chasing grizzly bears off their kills to have a snack. Indeed, this one (DH15DP) is solid, welded steel except for a rubber foot brace (which can be changed side to side). The blade has a sharp wedge tip and most definitely will not bounce off the ground. The 26-inch shaft is steel, and welded to the blade around the perimeter of the joint on both sides. It’s not the prettiest weld on earth—there’s spatter under the paint—but it’s not going to come loose. Likewise, the D handle is steel and welded.
It’s obviously not the lightest shovel you can buy, but its utility will extend beyond digging fire pits. Prying lodged rocks from under the frame rails of a high-centered truck should be no trouble. And the 15-inch blade offers plenty of surface area for scooping sand out from under a buried vehicle to insert Max Trax (there’s also a 12-inch version). Well-recommended.
Look for them here.
Hint: When using “Search,” if nothing comes up, reload the page, this usually works. Also, our “Comment” button is on strike thanks to Squarespace, which is proving to be difficult to use! Please email me with comments!
Overland Tech & Travel brings you in-depth overland equipment tests, reviews, news, travel tips, & stories from the best overlanding experts on the planet. Follow or subscribe (below) to keep up to date.
Have a question for Jonathan? Send him an email [click here].
SUBSCRIBE
CLICK HERE to subscribe to Jonathan’s email list; we send once or twice a month, usually Sunday morning for your weekend reading pleasure.
Overland Tech and Travel is curated by Jonathan Hanson, co-founder and former co-owner of the Overland Expo. Jonathan segued from a misspent youth almost directly into a misspent adulthood, cleverly sidestepping any chance of a normal career track or a secure retirement by becoming a freelance writer, working for Outside, National Geographic Adventure, and nearly two dozen other publications. He co-founded Overland Journal in 2007 and was its executive editor until 2011, when he left and sold his shares in the company. His travels encompass explorations on land and sea on six continents, by foot, bicycle, sea kayak, motorcycle, and four-wheel-drive vehicle. He has published a dozen books, several with his wife, Roseann Hanson, gaining several obscure non-cash awards along the way, and is the co-author of the fourth edition of Tom Sheppard's overlanding bible, the Vehicle-dependent Expedition Guide.